Edoardo Barbieri
on 28 October 2022
Accelerate IT/OT convergence in Industry 4.0 [Part II]
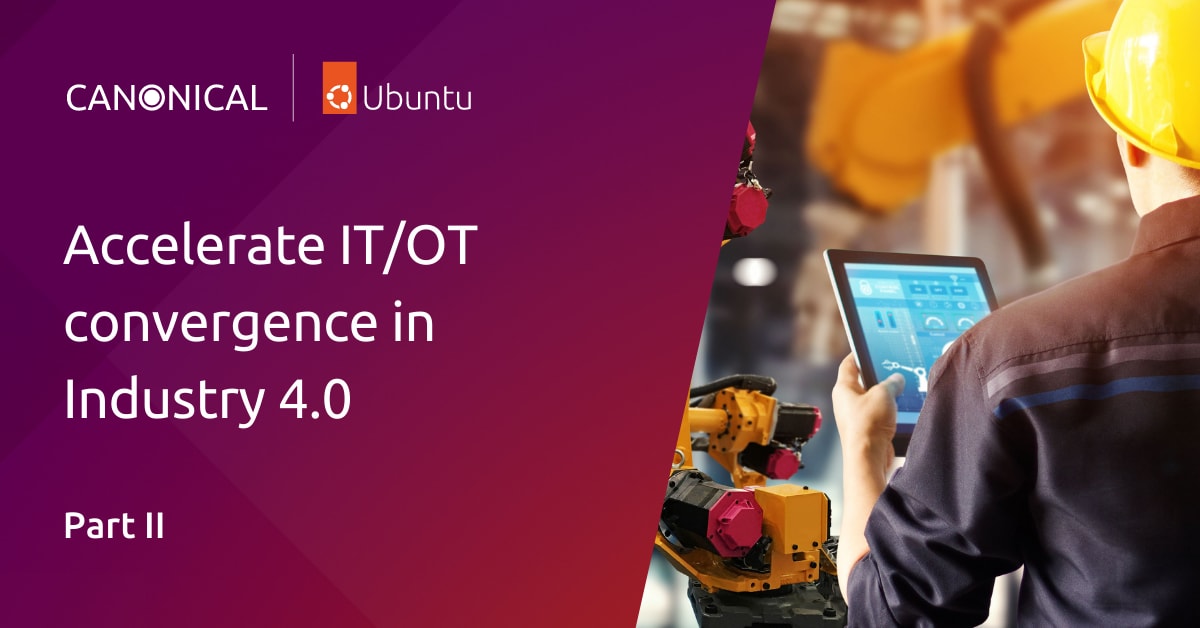
Welcome to Part II of this three-part mini-series on bridging the gap between operational technology (OT) and information technology (IT) in Industry 4.0. In Part I, we set the stage for the remainder of the series and gave an overview of IT and OT, the two technological layers of modern industrial factories.
In this blog, we expand on that knowledge by confronting the two domains and discussing the automation pyramid concept. In the final chapter of the series, we will make a case for how to close the gap and reap the benefits of Industry 4.0.
Without much further ado, let’s dive straight in.
Industry 4.0 hasn’t yet shown its full potential in industrial manufacturing because of the firewall between IT and OT, two technological domains siloed from each other. To fully benefit from the fourth industrial revolution and for digital transformation to materialise, manufacturers need to overcome the boundaries between machine controls from the OT layer, the IT world and the Internet of Things (IoT).
The picture is complex due to the inherent differences between the two domains. How can industrial players make it coherent?
The automation pyramid in Industry 4.0
IT and OT play different roles in automation and technological advancement in modern factories. The increasing computational power and horizontal specialisation of the 70s led to the rise of the automation pyramid.
The five layers of the automation pyramid are:
- Field level: The production or shop floor, where instrumentation like sensors, actuators, and motors lives;
- Control level: For sensing and manipulation, where PLCs and PIDs operate;
- Supervisory level: SCADA software for supervisory control and data acquisition;
- Planning level: The Manufacturing Execution System (MES) monitors the manufacturing process in the plant or factory;
- ERP level: Enterprise Resource Planning (ERP) or management level for business planning and logistics.
This strategic hierarchy was adequate for production planning and logistics processes in the early days. Today, however, this structure is no longer feasible as industrial manufacturers aim to unlock digital transformation by connecting all their resources, equipment, tools and machinery.
Stark differences and lack of technologies emerge when comparing modern IT and consumer technology to the operational technology world.
On the one hand, the IT ecosystem witnessed the advent of over-the-air (OTA) firmware updates. Similarly, secure application orchestration paradigms make every device software-defined and app-enabled, with an industrial machine intelligence ultimately a function of the software it runs. IT is synonymous with the latest technological advances, from app stores to speech recognition, modern programming languages like Java and Python, and version control with Git Hub.
Another clear difference between the two domains is the focus on security and networking. Also, IT often sits at the corporate level (CIO), whereas OT is organised locally at the plant engineering level.
On the other hand, modern factories still require costly manual interventions through on-site engineer visits down on the shop floor. Specialist programming languages like IEC 61131, or G-Code permeate industrial settings with the software decoupled from the hardware.
The lack of security and networking in OT is not feasible anymore as companies aim to accelerate their industrial transformation.
Overall, IT is living in 2022, whereas OT is still acting like it’s the 1980s.
IT/OT convergence in Industry 4.0
The convergence of IT and OT is a prerequisite for intelligent manufacturing, software-defined industrial systems, and next-gen smart factories. IT and OT need to collide to accelerate industrial transformation and seize market opportunities. The convergence is challenging because the two domains thus far worked separately and with different systems, technologies and vendors. Nevertheless, IT and OT are moving towards each other and overlapping.
The merging started with the Manufacturing Execution System (MES). Initially under the sole responsibilities of engineering teams and OT, MES now comprises standard networks and computers overseen by the IT department. The same holds for PLC systems, as they gradually adopt functionalities from the IT world. As IT is increasingly part of industrial manufacturing equipment and tools, those technologies that proved successful in IT will be adapted to provide value in the OT world.
With the automation pyramid and IT/OT firewall in mind, we now understand problems are more encompassing than siloed solutions, killer apps, or standalone adoption of AI/ML. Rather, industrial manufacturers and suppliers need a holistic approach to closing the divide.
Bridging the gap requires porting security, networking, visibility and transparency down at the shop floor and to manufacturing operations. Industrial pioneers need to monitor and control the physical devices and processes in the enterprise. The convergence between IT and OT calls for a transition from closed standards and interfaces to embracing open-source software and modern IT solutions.
Is a secure and interoperable platform, capable of OTA updates to devices in remote locations, too much to ask? How can we enable solutions across verticals to bring standardisation and homogeneity to the OT world? We will cover this in part III.
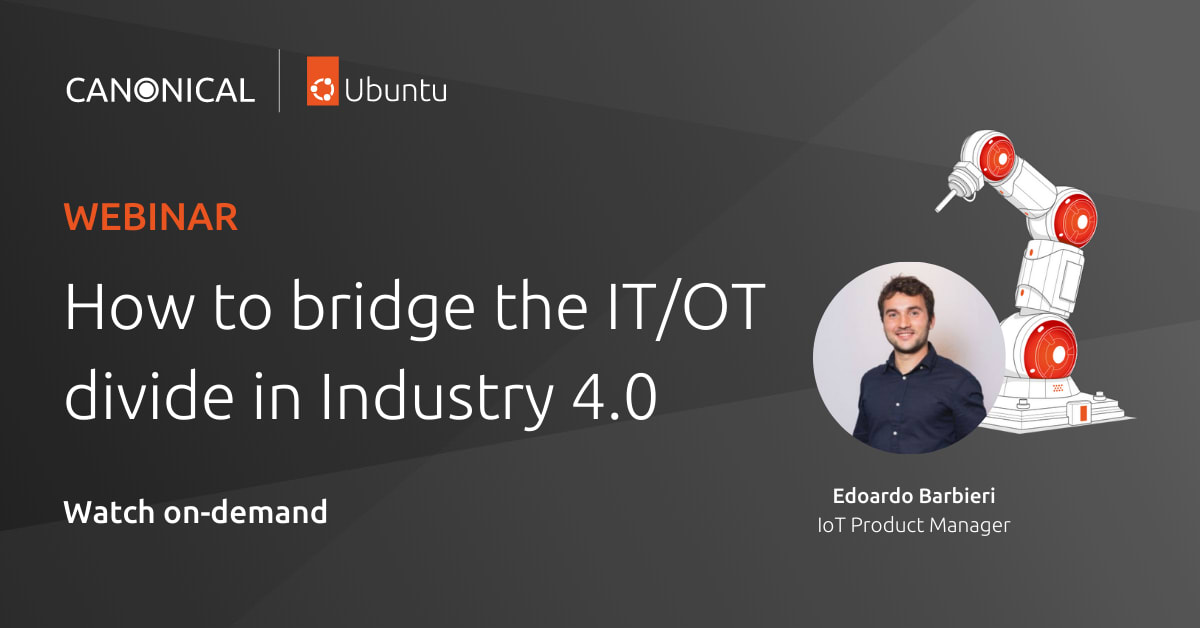
Interested in accelerating your industrial transformation and seizing market opportunity? Join our on-demandwebinar on how to tap into the fourth industrial revolution.
Further reading
Join the conversation on IoT Discourse to discuss everything related to IoT and tightly connected, embedded devices.
Why is Linux the OS of choice for IoT devices? Find out with the official guide to Linux for embedded applications.
Working on a new IoT project, but unsure which OS to pick? Learn about the trade-offs between Yocto and Ubuntu Core.
Did you hear the news? Real-time Ubuntu 22.04 LTS Ubuntu is now available. Check out the latest webinar on real-time Linux to find out more.