Edoardo Barbieri
on 25 October 2022
Accelerate IT/OT convergence in Industry 4.0 [Part I]
Welcome to this three-part mini-series on bridging the gap between operational technology (OT) and information technology (IT) in Industry 4.0.
Throughout this series, we will discuss the key challenges industrial manufacturers face when trying to accelerate their digital transformation. We will understand why legacy update approaches and lack of security in OT do not suit the Industry 4.0 world and assess how adopting open source software can help bridge the gap.
This is Part I, right at the beginning of the journey. We will start with the basics and offer a quick intro to the different domains playing a role in the industrial factory. In the second blog post of this three-part series, we will review the automation pyramid concept.
Part III is the concluding chapter of the series. We will make a case for why the convergence between OT and IT calls for a transition from legacy stacks with closed standards and interfaces to modern IT solutions and the embrace of open-source software.
With so much to cover, let’s dive straight into Part I.
The fourth industrial revolution fails to materialise
The term Industry 4.0 describes the journey of industrial pioneers toward a complete digital transformation across their value chains. The numbering refers to the three prior industrial revolutions, roughly coinciding with the invention of the steam engine in 1784, the use of electricity in 1870, and the first assembly line in 1969. We are now at the cusp of the fourth industrial revolution, driven by the advent of tightly embedded, connected devices and pervasive connectivity. In the past few years, enterprises have initiated many digital transformation projects to reap the benefits of Industry 4.0.
A series of self-reinforcing factors prompted this first wave of projects. The emergence of new promising technologies and use cases, from artificial intelligence to edge computing, attracted awareness in the market. Consequently, new use cases like remote machine monitoring and predictive maintenance promptly became the subject of public discussion. The growing enthusiasm among innovators and industrial pioneers then put a lot of pressure on all other players in the market to follow suit and adapt.
Unfortunately, the first attempts at accelerating industrial digital transformation fell short of their promise.
Purpose-built technologies applied as siloed solutions in an ecosystem with legacy install bases, and a lack of standardisation did not result in software-defined industrial systems and next-gen factories. A digital transformation approach via a killer app similarly ignores the fundamentals of modern industrial manufacturing facilities, with legacy machinery permeated by limited or no security.
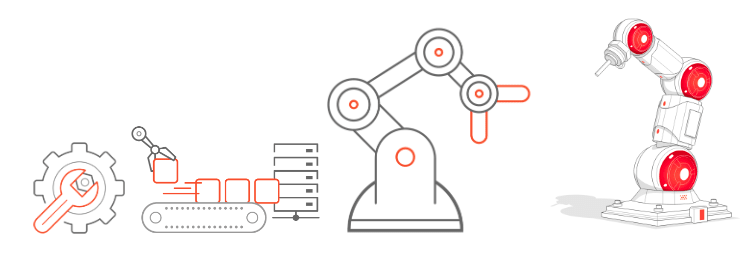
Throughout history, there have been three prior industrial revolutions. From the invention of the steam engine in 1784 to the use of electricity and the first assembly line in 1870, all the way to the invention of the first PLC in 1969.
After painfully learning the past lessons, do we now understand what it takes to tap into the fourth industrial revolution? The second attempt at accelerating industrial transformation promises increased overall equipment efficiency, new business opportunities and reduced TCO. As we face a new wave of IT in industry, the Industry 4.0 concept isn’t new, but unlike before, we now have the knowledge and technology for it to become an affordable reality.
From our present vantage point, we are in a better position to assess why those first attempts failed and know the problems are much deeper than just focusing on digitalisation or deploying a panacean killer app. We must instead bridge the gaps between the different domains playing a role in our modern factories. To grasp the challenges and blockers preventing Industry 4.0 from showing its full potential, we need to take a step back and discuss the status of the modern factory. Two different domains – OT and IT – play a role in modern factories. Let us assess them in the following sections.
OT in Industry 4.0
In industrial manufacturing, OT includes the hardware and software systems that control and execute processes on the shop floor. Similarly to how one often hears references to monolithic solutions and proprietary protocols, manufacturing systems, legacy machinery, SCADA software and PLCs are also commonly associated with OT. Among the main concerns of the OT ecosystem are machine and operation safety, determinism and real-time capabilities.
Operational technology is not homogeneous across its different facets. The lack of uniformity is due to the pervasiveness of specialised vendors manufacturing speciality systems and machinery. Overall, the OT is a horizontal layer optimised by component producers, with separate vendors responsible for their production.
The legacy infrastructure of the OT world often poses barriers to data sharing and 2-way communication between devices. Factory technicians did not connect speciality devices and OT machinery to a network during the early 90s, as the internet was not yet widespread. Those systems may have needed to talk to some other machine downstream in the production line, but not with the rest of the world.
Furthermore, suppliers in the industrial ecosystem addressed communication between devices by going proprietary. Lots of protocols then proliferated in the OT world. As industrial manufacturers expected their speciality devices to only ever talk to their other systems, they just made custom protocols. These days vendors keep those old protocols, as they want to be backwards compatible with their legacy equipment. Although some groups of vendors rely on a few protocols as a standard, the lack of homogeneity in OT is not comparable to the standardised TCP/IP of the IT layer.
The OT layer not being networked results in isolated communication means. Such technological backwardness is a blocker to the Industry 4.0 vision of a centralised location digitally connecting and collecting data across all systems, infrastructure and devices.
Machinery in OT is also not necessarily resilient. Often systems programmers did not ship good error handling code because of the tight resources on the devices. In those cases where the systems have enough resources to run a full-blown Windows or Linux distribution, the machinery is likely unable to undergo over-the-air software updates once set up. Manufacturers then need to install software on their PC for PLC troubleshooting.
Far removed from the OT layer, is IT, also playing a role in modern industrial factories.
IT in Industry 4.0
When referring to IT, one often considers networks, servers, laptops and the internet altogether. The standard networking and PCs in the office environment, IT is Information Technology as it concerns sending information from one person or machine to another in the form of data.
IT is almost at the opposite end of the computing spectrum than OT when considering its technological advances. From containers and orchestration to app stores and version control, updatability, scalability, and transparency are relevant features of the IT world.
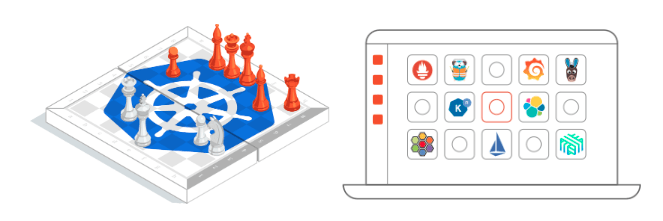
Robust communication and security are a cornerstone behind every IT strategy, which differs from OT over a few dimensions.
A further difference is in the level of conformity to standards. Although around 20 years ago, protocols were varied (some may remember IPX/SPX next TCP/IP), vendors, manufacturers and suppliers across the value chain converged to TCP/IP over the years. The level of uniformity in IT brings expectations around the transferability of knowledge. For instance, learning how to do TCP/IP in a corporate environment is transferable when working on another network instance, as, despite the different IP addresses, underneath lies the same standard TCP/IP.
One can further appreciate uniformity in IT when recalling the proliferation of different PC operating systems a couple of decades ago. The picture is very different today, as most enterprises have standardised their choice, picking Windows, Macs and Linux.
Final considerations to accelerate Industry 4.0
The gap between IT and OT needs to be closed to reap the benefits of the fourth industrial revolution. The convergence of IT and OT is challenging because these two worlds rely on different systems, vendors, technologies and standards. Nevertheless, closing such a divide is a prerequisite for smart manufacturing, autonomous industrial systems, and digital transformation in modern factories.
Stay tuned for part two, where we will further expand on the concept and discuss the automation pyramid.
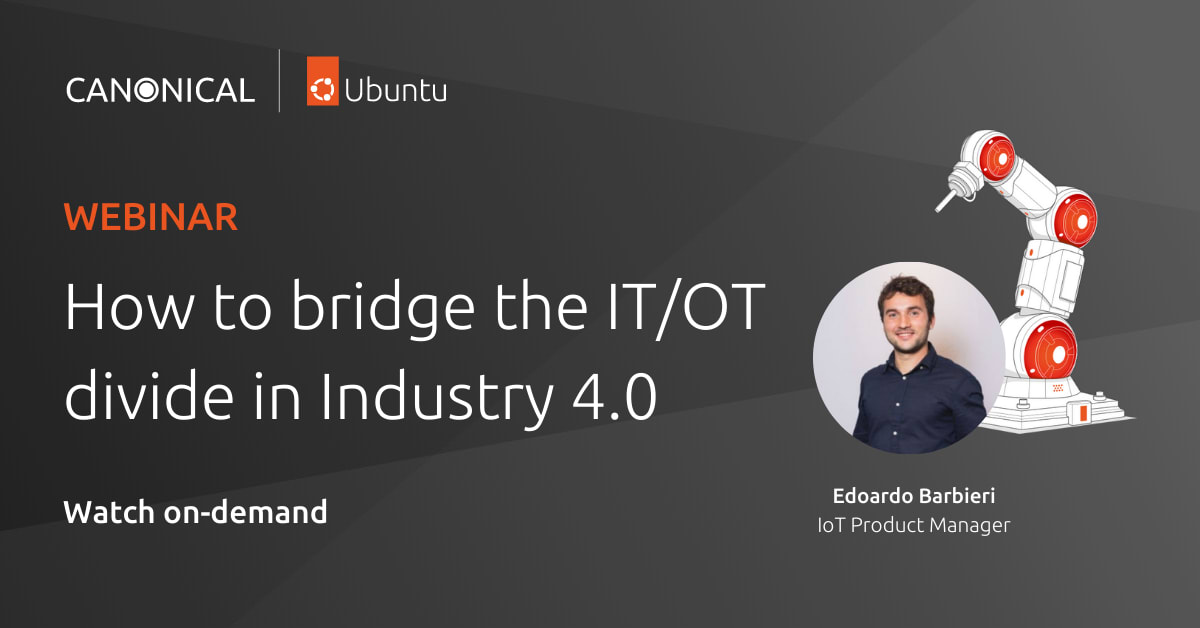
Interested in accelerating your industrial transformation and seizing market opportunity? Watch our on-demand webinar on how to tap into the fourth industrial revolution.
Further reading
Join the conversation on IoT Discourse to discuss everything related to IoT and tightly connected, embedded devices.
Why is Linux the OS of choice for IoT devices? Find out with the official guide to Linux for embedded applications.
Working on a new IoT project, but unsure which OS to pick? Learn about the trade-offs between Yocto and Ubuntu Core.
Did you hear the news? Real-time Ubuntu 22.04 LTS Ubuntu is now available. Check out the latest webinar on real-time Linux to find out more.